Há pouco mais de 15 anos contratei um colaborador para a farmácia onde trabalhava na época, para a função de auxiliar de serviços gerais.
Entre as atribuições da função estavam: limpeza da área de atendimento e escritório, das áreas de estoque e das áreas de produção.
Com o tempo esse colaborador, de nome Alexandre, desenvolveu outras habilidades, passando da limpeza para atividades auxiliares na produção, depois controle de qualidade, depois pesagem de sólidos, manipulação de semi-sólidos e líquidos, e por fim atuava em todas as etapas da produção e controle.
Conversando com ele a respeito do conhecimento que tinha acumulado durante seu tempo na empresa, perguntei qual a informação mais marcante que ele recordava, a primeira coisa que aprendeu na empresa, relacionada ao seu desenvolvimento, e a resposta foi: PANO SUJO NÃO LIMPA.
Após segundos de surpresa com a resposta, ouvi a explicação sobre ela: quando iniciou as atividades na limpeza, essa frase deu a ele a direção para executar bem as tarefas de sua responsabilidade. Antes de iniciar a rotina de limpeza dos ambientes ele checava todos os utensílios, os panos, baldes, produtos das soluções sanitizantes, para ter certeza de que tudo que fosse necessário para a execução da tarefa estava disponível e em condições adequadas ao uso. Caso ele aparecesse na área de trabalho com um pano cinza, a “bronca” era certa, rsrsrsr.
Esse critério serviu de ponto de partida para cada nova tarefa aprendida, trazendo o mesmo conceito de organização e excelência.
Transpondo essa experiência para o conjunto de operações da produção magistral, fica bem claro que era uma aplicação prática do sistema 6M de Ishikawa, de modo reverso, digamos assim.
Essa ferramenta, usada para rastrear a causa raiz de uma não-conformidade, reúne seis condições que devem ser investigadas. Logicamente quando estas condições são atendidas com excelência afastamos a possibilidade de intercorrências.
O conhecido diagrama espinha de peixe reúne os 6M que devem ser avaliados:
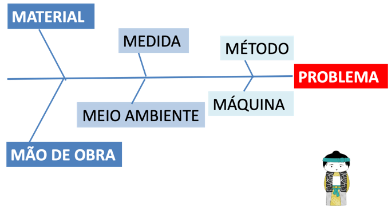
A análise é feita de modo retrospectivo, a partir do problema detectado, buscando o ponto de origem, para iniciar o processo de aplicação de medidas corretivas e preventivas.
Podemos então, como fez intuitivamente o Alexandre, partir da verificação prévia dos 6M para assegurar um resultado excelente.
Vamos à descrição:
- Método: como a maneira como o trabalho é realizado afeta o problema?
- Máquina: como os equipamentos utilizados no processo influenciam o problema?
- Medida: como as métricas utilizadas para medir o desenvolvimento da atividade influenciam o problema?
- Meio ambiente: como o meio em que a atividade está sendo desenvolvida influencia o problema?
- Material: como a qualidade e o tipo dos materiais utilizados influenciam o problema?Mão de obra: como as pessoas envolvidas na atividade influenciam o problema?
Em resumo, para cada um dos M citados, quando agimos de forma preventiva, ou melhor, proativa, garantindo as condições ideais para o trabalho proposto, o resultado certamente atenderá os requisitos de qualidade estabelecidos, e este modelo traz vantagens muito interessantes para a empresa:
- Garantia de uniformidade e padronização de processos – MÉTODO.
- Máximo desempenho dos equipamentos – MÁQUINA.
- Geração de registros efetivos – MEDIDA
- Condições ambientais estáveis – MEIO AMBIENTE.
- Especificação de insumos e critérios de qualidade – MATERIAL
- Qualificação da equipe com treinamentos específicos – MÃO DE OBRA.
Os conceitos, métodos e vantagens estão descritos, mas a aplicação é, sempre, uma decisão estratégica indelegável – você, gestor, é quem decide o caminho e prepara as condições para evoluir.
A pergunta que deve ser respondida é: teu pano de chão está limpo?
Gelza Rubia Rigue de Araujo – Consultora Farmacêutica